Some of the links shared in this post are affiliate links. If you click on the link and make a purchase, we will receive an affiliate commission at no additional cost to you.
The company was founded in 1991 by James Dyson and is world-famous for its vacuum cleaners and fans. They stand for quality and design, which is not cheap. The founder announced in 2017 that they wanted to launch a functional electric car by the end of 2020. More than 400 employees have worked on the project and the company has invested 2 billion pounds in the project. Over time, the team has grown to a total of 700 employees. As the company announced, the project was canceled in 2019. Why did Dyson want to follow in the footsteps of electric car pioneer Tesla and above all? Why was the project scrapped?
Why did James Dyson want to build an electric car?
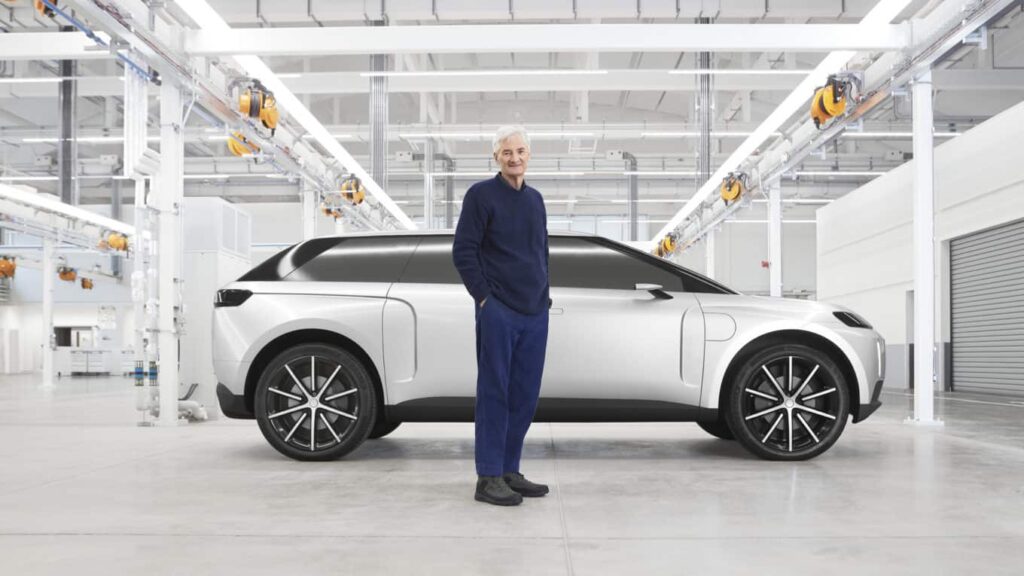
Even as a child, I was always horrified by the black cloud of smoke rising from the back of cars. Recently, gasoline and diesel engines have become less smoky, partly because the particles have become smaller; it looks better to the naked eye, but they are still not free of dangerous gases. Nevertheless, the problems with combustion engines and diesel exhaust particles continued to be ignored by traditional car manufacturers and governments. Tesla began to look seriously at electric cars […]
James Dyson
James Dyson visited a spin-out company at the University of Minnesota in 1983, at the beginning of the development of his cyclone technology for particle separation. They had developed an aerodynamic particle counter because he needed to measure the effectiveness of my cyclones for particles as small as 0.01 microns. During the visit, they showed him a copy of a US Bureau of Mines report on diesel particulate emissions from US mines.
The report showed that laboratory mice and rats were suffering heart attacks, cancer and other serious health problems when exposed to diesel fumes. As engineers, he couldn’t ignore this, so James Dyson began developing various particulate capture methods using cyclones and other novel technologies.
After years of development, Dyson had its own technologies in the field of electric motors and batteries. So James Dyson went back to the old problem and tackled an electric car. Dieselgate changed everything.
Because all car manufacturers had no choice but to switch to electric vehicles – almost overnight. Electric cars are considerably more expensive to produce and manufacturers make large losses on the sale of individual cars. These losses are less important to them because the sale of electric cars allows them to offset them against the sale of traditional vehicles, on which they make a good profit. As a technology-based car – being developed by a non-automotive manufacturer – we realized that our car was suddenly no longer commercially viable. It was a difficult decision to stop because hundreds of engineers, scientists and designers had put everything into the project and it was a great technical achievement. But I have no regrets about starting the program. We learned a lot, and Dyson benefited from a huge influx of engineering talent from the automotive industry – it was quickly applied to other areas of our research and development.
The electric car from Dyson
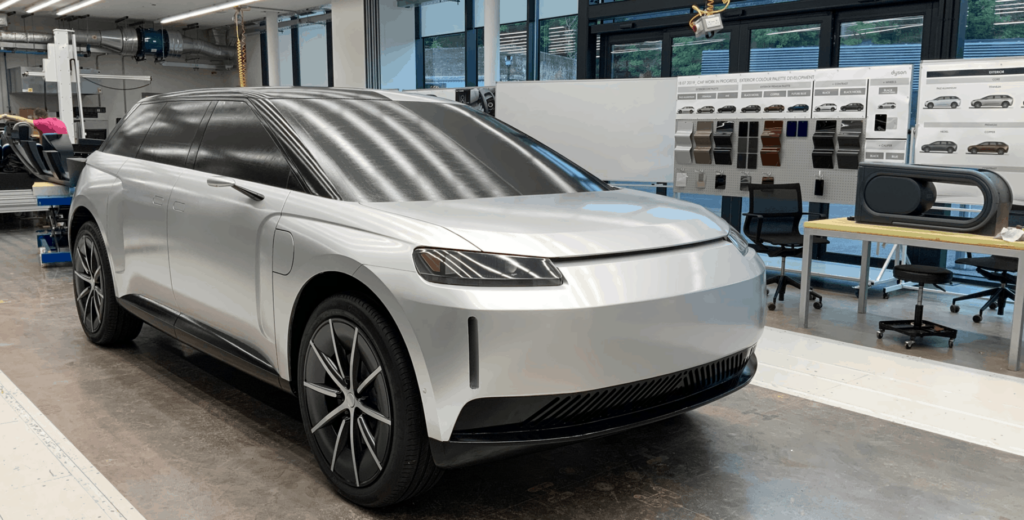
Dyson developed the car from the ground up, the company refrained from using ready-made parts from other manufacturers. The car was designed as a platform. The body can be modified, while the chassis remains the same. The first model was an SUV. During high-speed driving, the car pushes itself down to provide less drag and better ground contact.
When I drove our car for the first time, I felt the same way as when I used our hairdryer prototype or the vacuum cleaner for the first time – I enjoyed it, but it didn’t surprise me, in fact we immediately looked for improvements! When you’re involved in the design and development of every little detail of a product, it takes away the surprise of seeing or using it for the first time. – James Dyson
The car is exactly five meters long, with thick tires and high ground clearance. This is helped by the fact that the underbody is completely flat. The wheels are actually one of the most interesting aspects; because of their size you have less rolling resistance and it’s easier to drive on bumps and potholes – it’s exactly the opposite of a Mini. The wheels are right in the corners and I don’t think you’ll find another car with the rear wheels so far back. The placement and size of the wheels brought some unexpected benefits in terms of comfort and road holding.
Motor and battery
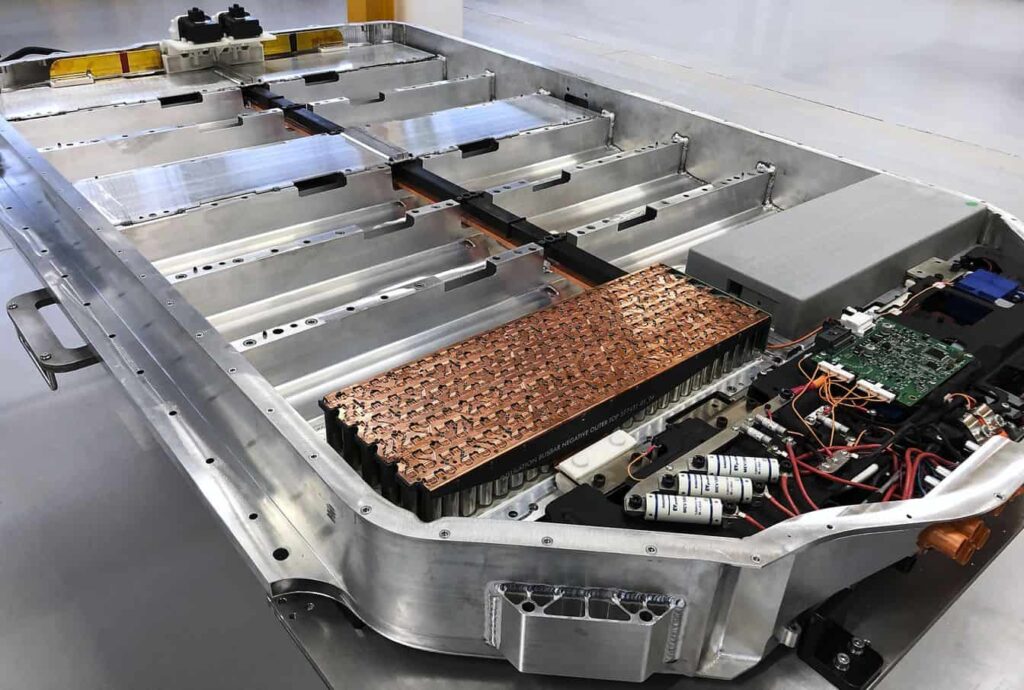
Building on Dyson’s years of experience with Dyson Digital Motor technology, a bespoke, integrated and highly efficient Electric Drive Unit (EDU) was developed, consisting of a Dyson digital electric motor, a single speed gearbox and a state of the art inverter. These compact and lightweight units were mounted on subframes at the front and rear of the vehicle.
The high-capacity battery pack assembly has been designed as an integral part of the body structure to optimize both weight and space available for occupants in the cabin, while providing the required rigidity and impact protection. The aluminum battery pack housing has been designed to be flexible so that a variety of possible sizes and types of battery cell solutions can be installed throughout the life of the vehicle platform without the need for significant redesign.
Cladding & interior
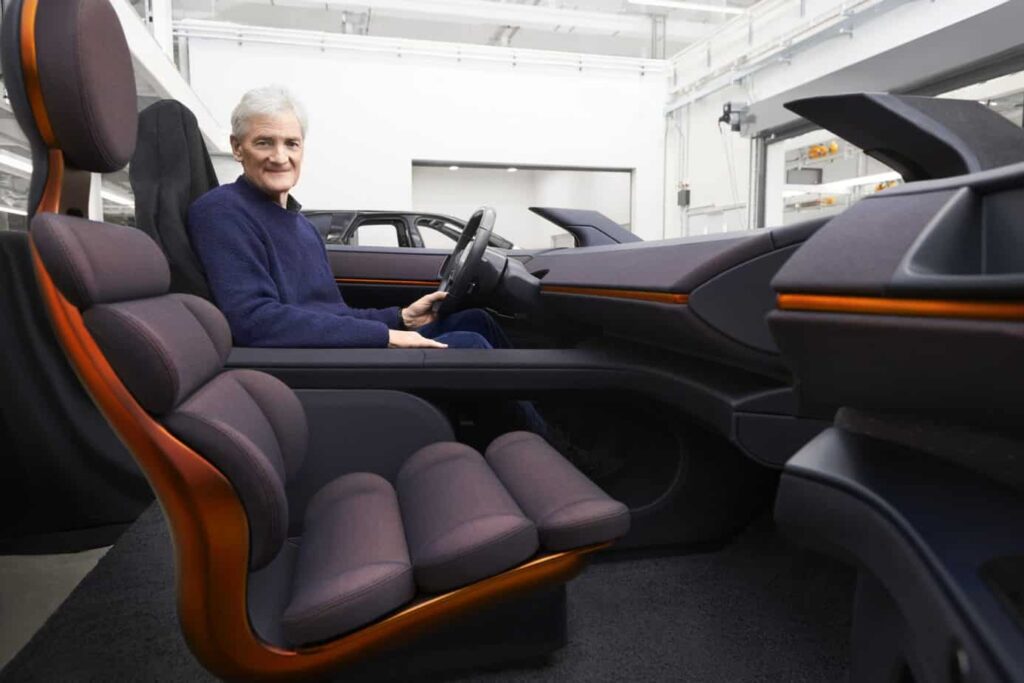
The car has three rows of seats in which seven adults can sit comfortably. The classic car seat has been dispensed with. Instead, a specially developed design is used that has appropriate lumbar support.
Dyson filter technology is also used in the car. All controls are located on the steering wheel. Unfortunately, the project was terminated. With these ideas, a high-quality electric car could certainly have been developed.